GN mining vibrating screen, shale shaker and decanter centrifuge, desilter cleaner are used for Australia construction mud treatment. The construction mud treatment system including:
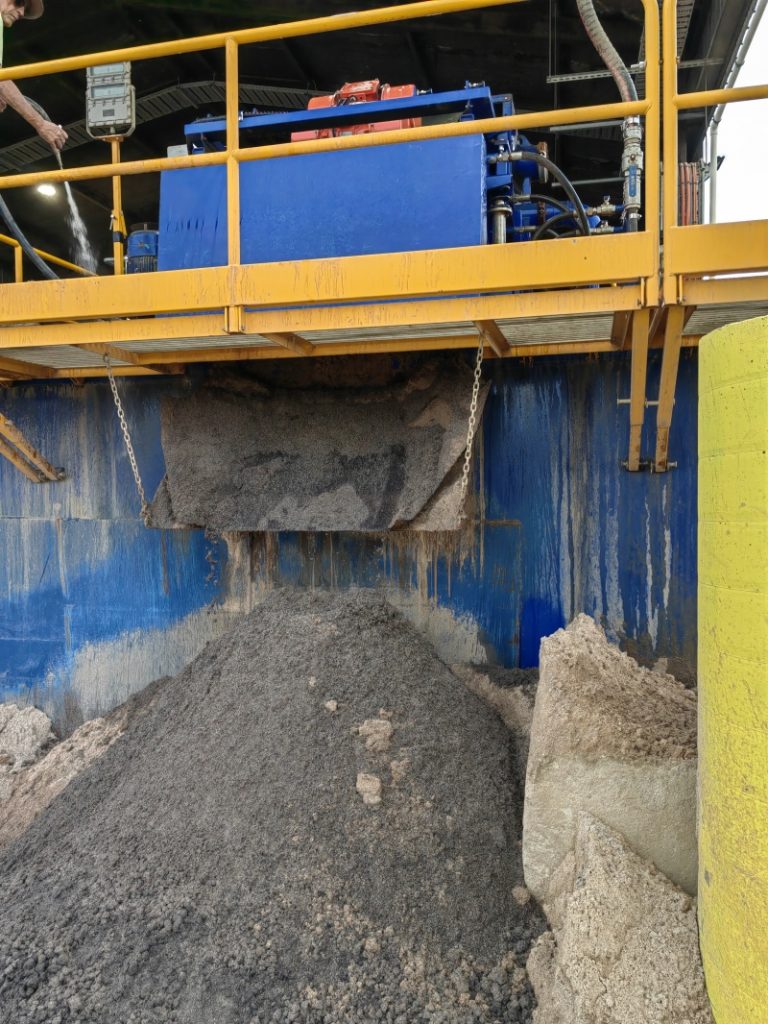
Mining vibrating shaker , the function is to separate stones, construction waste, branches, etc., so that big solids will not be feed to further process and block the equipments.
The high frequency fine vibrating screen, the function is to separate the coarse solids and reduce solids content. The composite material frame shaker screen is used to separate the coarse solids from to construction mud. We can produce different API mesh size screen from API 20 to API 325 according to your requirement. The high frequency fine vibrating screen is designed for classification, separation and dewatering application of wet or dry screening.
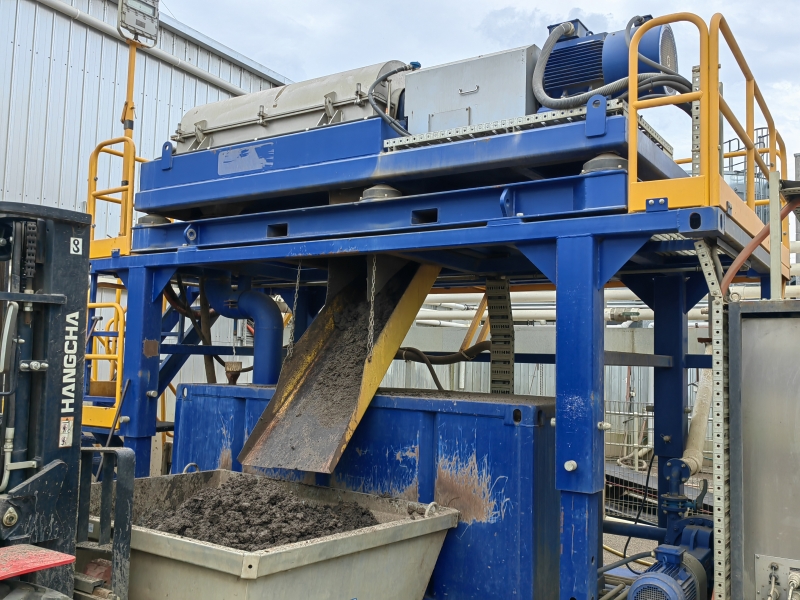
Desilter mud cleaner, the function is to separate the fine solids from the construction mud, the separation cut point is 15~40 microns. The qty of desilter cone depends on required treating capacity. The bottom shaker installed composite material frame shaker screen for drying the discharged solids and recycle more useful fluids.
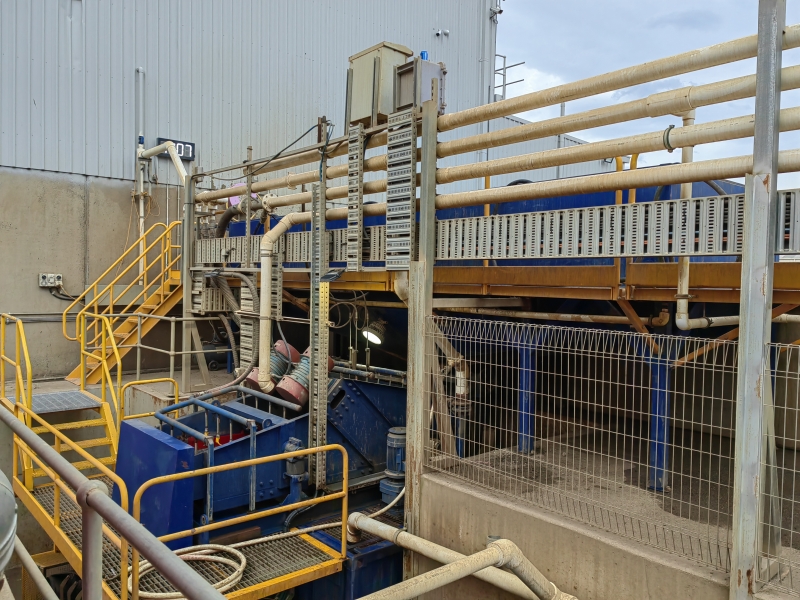
Decanter centrifuge, the function is to separate the fine solids cut point 2~5 microns, working with flocculants from chemical dosing unit, most of the ultra fine solids can be separated out, the recovery water can be reused or sent to waste water treatment plant for further treatment. The previous separation has separated most of the coarse solids and reduce solids content to proper content so that the centrifuge can work properly without blocking the screw.
The solids discharged from mining vibration shale shaker, high frequency fine vibrating screen shaker, desilter mud cleaner, decanter centrifuge can be collected by waste collection box and easily transported to other place. If you need a customized construction mud treatment plant, pls contact with GN solids control.
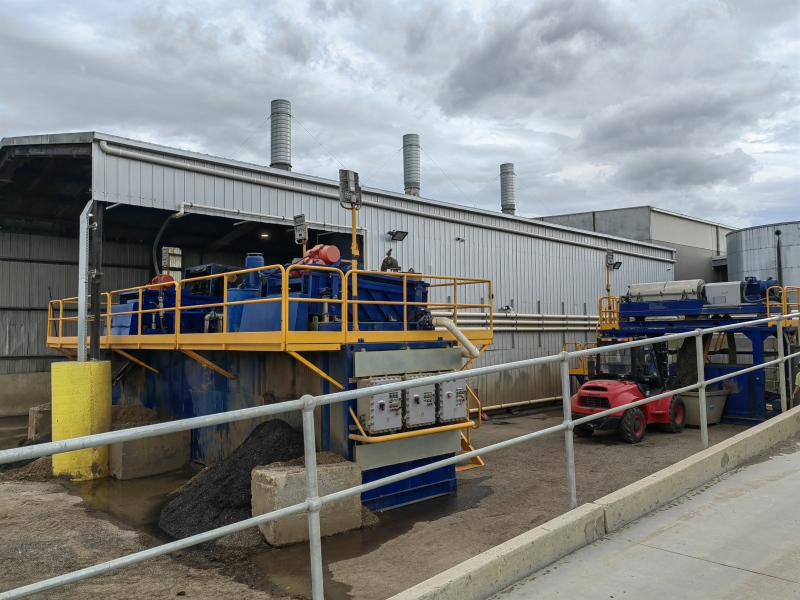